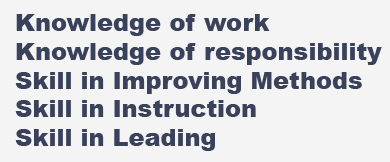
TWI Training Solutions Inc.
is the premier provider of and resource for your
leadership and employee training improvement needs.
Focusing on satisfying the five needs of a leader.
This is accomplished by
analyzing your businesses challenges and applying the
appropriate tools, training, and coaching in a TOTAL
solution model addressing.
Job Instruction (JI) is a streamlined method of
instruction. Using key tools such as, the four
step method and the five needs of good
supervisors, JI aims to reduce training time,
reduce scrap and rework, limit workplace
accidents and increase overall job satisfaction.
Over an, easy to digest, 5 two-hour session
trainees will learn tools to help them in their
objective to become good supervisors. JI will
help your company get the “know how” over,
quicker and easier providing both, new and
experienced workers, knowledge to get a person
to quickly remember to do a job correctly,
safely and conscientiously.
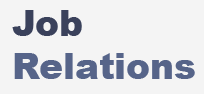
Job Relations (JR) builds positive employee
relationships while increasing motivation and
cooperation and effectively resolving conflict.
The four step method taught in this module of
training teaches not to jump the gun when it
comes to your employees. With the process of
getting the facts, weight and decide, take
action and check results, companies can maintain
good working relations and achieve increased
productivity, improved attendance, better morale
and higher employee retention rates.
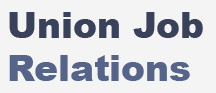
Union Job Relations (UJR) follows the same
ideology and principles as Job Relations with a
customized plan for union stewards and leaders.
The foundations and four step methods are
modeled around creating positive union
relationships.
Job
Methods (JM) aims to produce greater quality of
products in less time by make greater use of
people, machines and materials currently
available. Trainees are taught how to breakdown
their jobs into their constituent operations.
Every detail of the job is examined to determine
room for improvement.
New methods are developed by eliminating,
combining, rearranging and simplifying steps in
the process. Using JM companies have reduced
cost through productivity gains, increased
throughput, and reduced work in process.
One
of the things trainees learn about in Job
Instruction is key points. Key points are NOT
the work sequence, but the "how-to" of the job
and key points are the focal point for Job
Safety (JS).
In JS trainees will learn how to analyze safety
hazards, spot hazards standardize the job,
improve communication, train people to think
systematically safety, and get people to see the
link between standardization and safety.
Companies that have put JS training into
practice have seen an 80% reduction of
accidents.